With the development of industrial automation and logistics technology, the market demand for high-tech is increasing. Machine vision technology is helping to upgrade the automation of the logistics industry, and the logistics industry is evolving rapidly from intensive labor to intelligence and automation. Become one of the most active areas in automation technology. At present, machine vision is widely used in the fields of sorting, measurement, storage, and warehouse management. Not only can greatly save labor costs and improve overall efficiency, but also greatly improve the utilization of transportation and storage space, which can significantly reduce unit transportation costs.
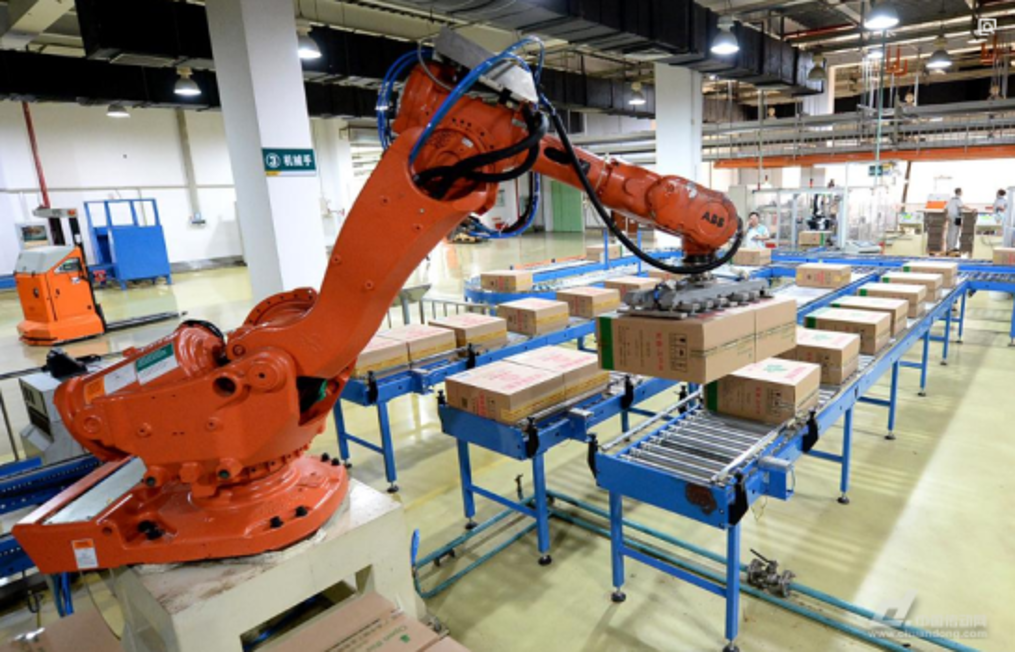
Take the common demand for destacking and palletizing of cage trucks as an example, because the SKUs faced by the logistics industry are always highly disordered and random, and have high requirements for system processing speed and throughput, and for visual recognition, positioning, and Robot grasping has brought great technical challenges. Together with leading partners, Tuyang has developed and implemented a large number of sites for major customers in multiple industries. The capabilities and products have undergone sufficient verification and have a significant market share. Leading position.
Based on the industrial 3D camera hardware + intelligent software algorithm independently developed by Tuyang, through AI, 3D vision, and deep learning, the robot can break through the limitations of use. The robot can successfully identify a variety of commodity packaging, logistics boxes, parcels, and other objects without prior learning, even if the commodities are stacked randomly.
The 3D machine vision guided depalletizing scheme is as follows:
Use 3D machine vision (hardware + software) to quickly and accurately obtain three-dimensional data information of objects on conveyor belts and pallets, and send positioning coordinates to the robot through Gigabit Ethernet to guide the robot to quickly pick up or stack. Unload (or grab) items such as boxes, packages, bags, etc. from pallets or conveyor belts one by one, and place (or stack) them on pallets or conveyor belts as required; Tuyang visual depalletizing solutions have been widely used in electrical appliances manufacturing, logistics, Automated production lines and logistics warehousing in food and other industries.
The machine vision positioning recognition system is composed of one or more 3D cameras. The field of view (FOV) and measurement range (MR) cover the entire material frame or stack. The 3D camera is used to carry out the high-speed movement of the basket or stack on the conveyor line. Photograph recognition, obtain the three-dimensional information of the object, and calculate the three-dimensional data of the object through the three-dimensional vision software algorithm. After obtaining the three-dimensional data information of the object, enter the “3D image processing module” to segment each individual piece of goods through the three-dimensional features of the object, and extract the most suitable grabbing pose of the goods, so that the robot can quickly and Grab the goods accurately. Then use the “Image Coordinate Conversion Manipulator Coordinates” module to convert the best grasping pose of the goods previously obtained to the manipulator coordinate system, and transmit the coordinate data to the robot through the visual communication protocol, and the robot control module controls the robot to perform the grasping action.
This application solution system also has the following features:
High-precision positioning guidance, precision control <5mm; Automatically identify multiple SKUs, no need to manually switch project files; Visual processing per beat <1.5s (Picture -> Calculation -> Output Coordinate)
Stable performance, high efficiency, cost-saving, accuracy up to 98%;
The standardized scheme can quickly complete the installation and deployment;
The solution has the advantages of being able to cope with mixed depalletizing and disorderly sorting; simple debugging and a high degree of automation, which can meet the depalletizing needs of the logistics industry and factories, and further improve production efficiency.